What does brass forged mean?
Brass forging is to press brass raw material by a brass forging machine. To make it have the property called plastic deformation. To have certain mechanical properties, shapes, and dimensions. By the method of forging can eliminate the flaw of forging porosity during the brass smelting process. Optimizing the microstructure. At the meaning time, due to saving the universal brass streamline, the mechanical properties of brass forged is better than brass cast.
The original state of material for brass forging parts
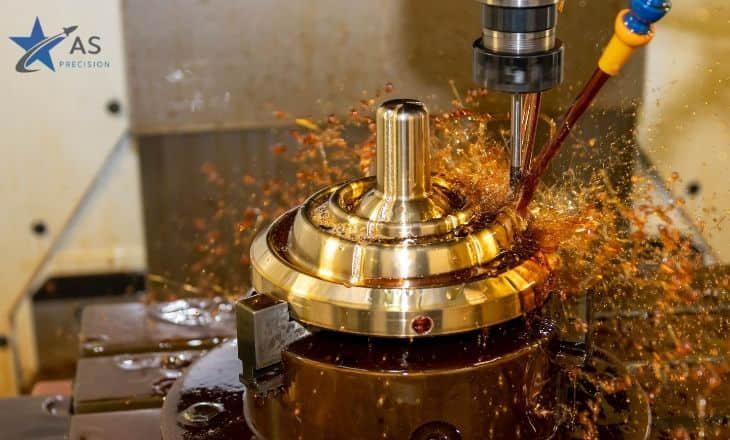
Bar, ingot casting, brass powder, and brass liquid are the 4 original
states for brass forging material. The ratio of the cross-sectional area before
and after brass deformed is called the forging ratio. Choosing a correct
forging ratio, proper heating temperature and preserving time, proper initial
forging temperature and final forging temperature, proper deformation value,
and deformation speed, all can improve the quality of forging brass parts and
decrease costs.
Normally, raw material for small and medium brass forging parts is cylindrical or rectangular bars. Bars have fair and fine grain structure and mechanical properties. AS PRECISION company can do batch production with bars that have correct dimensions, right shape, and good surface finishing. Keep in mind that with controlling properly brass forging temperature and deformation conditions, no use of big forging deformation can forge excellent brass parts out.
Difference between brass forging and brass casting
Technique difference:
- Brass forging and brass casting are 2 different techniques.
- Brass casting is a process of pouring melting brass into a mold, then cooling it to become a solid state. It’s usually using a power hammer to beat and hit, then make brass parts out. Basically, it’s a process of solid to liquid to solid.
- Brass hot forging is plastic deformation under solid state, is to use a brass forging machine to press raw materials with high temperature. Based on this, it can refine the grain and change its physical properties. Literately it’s a process of solid to solid.
Performance difference:
- Brass raw material through the way of plastic deformation has the effect of refining grains, therefore, it’s often used for important parts in brass raw material fabrication.
- Brass casting has a requirement for processing material and doesn’t have as many advantages as brass forging. During the process of casting, despite having porosity, it’s easy to make complex brass parts. Thus, it’s used in rough brass raw material fabrication.
Is brass good for forging?
Brass is greatly forgeable. It’s an alloy that contains various
percentages of zinc, copper, and other metals. With various components, brass
has some typical features, such as listed below:
- Easy recycling: brass is usually reused and remelted to get an ideal shape.
- Top brass aluminum corrosion resistance: brass is not easy to be rusty because it’s a nonferrous alloy.
- Wide temperature range: the hot forging process with a moderate temperature can allow a major tolerance and simply work considerably.
What tools are needed for forging brass parts?
- Forging machine or press machine.
- Gas stove or electric stove, temperature range from
750℃ to 880℃, equal to 1382℉to 1616℉. - Mold dope cylinder and Double holes spray gun.
- Mold dope.
- Two-sided heating flaming gun.
- Tongs.
- Special shape forging die.
Procedure for brass forging parts
Preparation for forging:
- Fuel modest oil to each oil port, and pump up air pressure to 6-8kg.
- Make sure the mold dope cylinder has ready-made mold dope.
- Make sure the cold and burning functions are normal, and whether there’s an air leakage at each port.
Die alignment:
- Fuel modest oil to each oil port, and pump up air pressure to 6-8kg.
- Make sure the mold dope cylinder has ready-made mold dope.
- Make sure the cold and burning functions are normal, and whether there’s an air leakage at each port.
Die alignment:
- Check whether the die is cleaning, then pinpointing punching hammer and die.
Operation:
- Pre-heating the die for 20 to 25 mins, heating the raw material to 730℃ to 810℃ (1346℉ to 1490℉), only for reference, specific to prevail in specific needs.
- The operator supposes to stand at the center position of the forging machine with a spray gun on the left hand, and a pair of tongs on the right hand.
- Aiming at the die to spray evenly one time or two times, make sure the forging parts can easily get off. If there is a pattern shape, the less mold dope, the better, ensuring no crumbling happens.
- Do put too much pressure on the heated brass raw material, as long as you can hold it tightly is good enough.
- The raw material needs to be put in a fixed position in the die. The quicker movement, the better. To avoid dramatic temperature decreases.
- Waiting for the forged part to be done, take 200% of carefulness to withdraw it with a pair of tongs from the part’s edge. Slightly take and put, the part is vulnerable at this phase due to its high-temperature state. After cold enough (about 1 minute), put it to the runner.
Safety caution:
- Safe operation is very crucial. Always stay focusing while operating, keep your eyes on 100%.
- Especially be aware not to scald yourself.
- Safety button on first before you put your hand into the forging area.
How to evaluate whether forged parts are good or not?
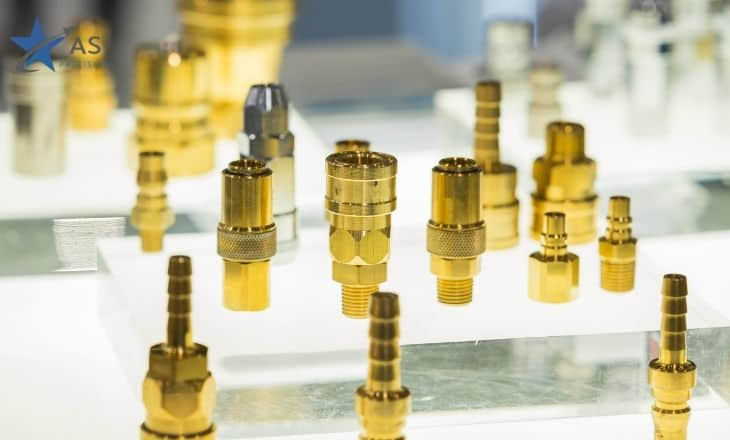
Shortage of material is because the raw material can’t fill the eternal
entire body. Reasons:
- The design of die is wrong.
- The temperature of die is insufficient.
- The stiffness of raw material is harder.
- The temperature of raw material is insufficient.
Cracks:
- The raw material has cavities or impurities.
- Trimming dragging.
- The R corner of the die is too straight.
- Position of the raw material to the core of the die.
Deformation is because of the effect of thermal expansion and cold
contraction while the material becomes thin after heating and heavily pressing.
Deformation within 0.3mm is a normal stress variation. Reasons:
- Wrong use of mold dope.
- Wrong taking of material withdrawing.
- The die is not in the center position.
Pockmarks are due to dirty things created when the material is completely
formed. Reasons:
- Excessive carbon accumulation.
- Didn’t clean off copper powder on the surface of the raw material.
- Impurities in the raw material are too many.
- A layer of oxidation. Usually wash off the oxidation layer with the sulphuric acid before inspection will have an ideal surface.