What does CNC machining mean?
CNC machining usually means a computer numerically controls precision machining tools to machine parts on a CNC lathe. In spite of the working procedure being basically the same compared to CNC lathe machining to conventional lathe machining, the change is obvious. The method of machining operation for using the numerical system to control parts and cutting tools access is an effective way to solve problems, like variousness, small batches, complex features, high accuracy. Achieving high efficiency and automatic machining.
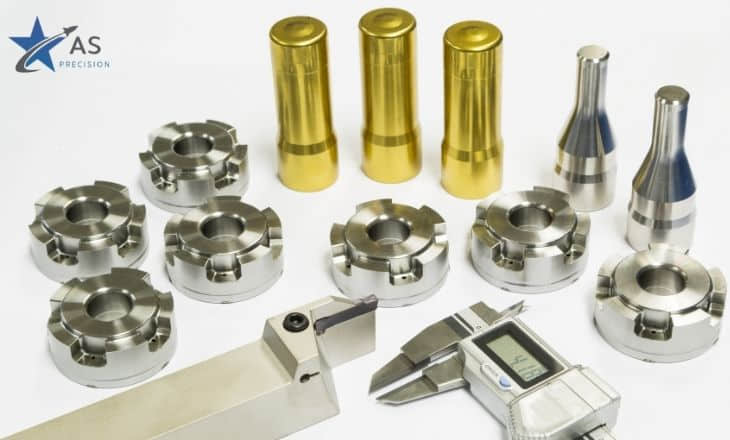
What are CNC machining parts?
A CNC machining parts supplier can supply various forms of parts regarding customers' needs. Common materials used such as stainless steel, brass, titanium, aluminum. Not even materials' properties are a vital matter, tolerance and surface treatment are also important factors.
Different CNC materials have different purposes for a CNC milling machine
and a CNC turning machine.
How to design CNC machining parts? Realizing how parts are CNC machined can help set up a clear understanding of parts design. There are 6 aspects we need to know about for design restrictions.
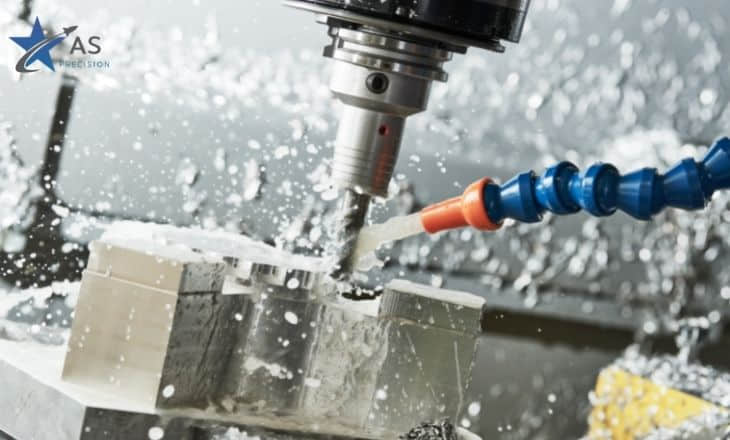
- Cutting process
- Tool geometry
- Tool access
- Workpiece stiffness
- Tool stiffness
- Workholding
1. The cutting process needs to follow these 4 rules below:
- Ensuring accuracy.
- Making the CNC route the shortest to affiliate the machining efficiency.
- Simplifying computer numerical workload, simplifying machining procedures.
- Using a subprogram to replace the repeated program.
2. Most of the tool geometry normally is cylindrical. That restricts the CNC parts' geometry. If you want a vertical sharp corner in CNC parts. It's unfeasible. No matter how small the cutting tool is, the parts always have radius corners.
3. Tool access. The geometry with a limited depth and undercut that cutting tools can't reach cannot be CNC machined.
4. Due to strong cutting forces and heat, workpieces might vibrate and deform.
5. For the same reason, you could have looser tolerances because cutting tools deform and vibrate during the CNC process. Tool stiffness is prominent.
6. Workholding - the shape of parts determines the way be held on the CNC lathe, which could lead to a serious impact on accuracy and cost.
As you may know, CNC is a great way to create a prototype and production
parts. It’s fast and cost-efficiency. But, it has advantages and disadvantages.
For taking its advantages ultimately, we have to take the essence into designs.
Bear that in mind, considering the index of holes is crucial. It’s due to many
CNC machining parts suppliers would use an end mill rather than a drill bit.
Because of that, the radius of holes is more flexible, and the cutting tool has
wider machining space. Then it’s possible to get a better surface finish than
with a drill. CNC machining also can use a cutting tool as a machining slot and
pocket, in order to decrease the processing cycle and costs. The only drawback
is when the ratio of depth to cavity’s diameter is over 6 times, it’s pretty
hard to be CNC machined. Plus, the length of an end mill is limited. If the
cavity’s depth is over the end mill’s length, the end mill is required to
machine through from both sides, which is wasting time and costing money.
Another is thread making. There is a more progressive approach called thread
mills. They can cut high-accuracy threads. For any threads with the same pitch,
a single drill is enough. We can benefit from saving a lot of production time
and tool setting time. Therefore, metric threads from M2 to M12 are
recommended.
Next part, the height and size feature of the parts. As far as we know,
even the strongest cutting tool would deform or vibrate, which might lead to a
tolerance error. During the CNC manufacturing process, workpiece and cutting
tools are prone to vibrate or break if the cutting tool has a bigger ratio of
length to diameter.
For lessening the positional error to have higher accuracy during machining, when you manually reposition, it’s not negligible. That’s why a 5-axis CNC machine is more progressive than a 3-axis CNC machine straight from the horse’s mouth. With 5-axis CNC machining, it allows you to machine parts with peculiar designs from more flexible angles. Well known for that traditional 3-axis machining, the workpieces are held from the bottom and cut from the top. Therefore, every piece needs to replace twice, each time on one side. However, a 5-axis machine allows the parts to rotate at the X and the Y axis, up and down, left and right, forth and back. As it turns out, no matter what kind of complicated workpieces can be well gripped, and any kind of geometry can be done.
7 tips for reducing costs on CNC machining.
High costs for CNC services or custom machining services can be a real
deal breaker. To minimum costs on custom machined parts is prominent for
factories to survive in the jungle. Check out the list below, and see what we
can do.
Tip 1: Machining time and model complexity are major factors. The more
complicated, the more expensive the CNC parts will be. Simple geometries and
standardized features are good ways to stick on.
Tip 2: Reducing unit cost by manufacturing bulk orders.
Tip 3: If you want to make words on parts, it’s better to be recessed
rather than raised. Apparently, it’s way too easy for removing rather than be
on the parts.
Tip 4: Using CNC milling tools to cut radii at internal vertical edges,
the larger, the better, recommended at least 1/3 of the depth of the hole.
Tip 5: Deeper depth of cavities influence crazily on costs. And even bring
tools breaking or deformation. Limiting the depth definitely is a good method.
Tip 6: Avoid cutting tools or workpieces break off. Choosing suitable
matching pairs.
Use T-shaped, V-shaped, lollipop-shaped, or custom cutting tools for the
surfaces where straight tools can reach.
Tip 7: The working procedure with the same installation or a single cutting tool, using a subprogram to replace the repeated program, making the procedure is continuous, in order to avoid error from the workpiece repositioning or the cutting tool replacing.
Where to find a CNC machining parts supplier?
AS PRECISION is a company offering CNC machining services in China, specializing in offering high precision CNC machining services and parts. It has been doing this industry since 2005 in China domestic and global market. Covering 5 axis CNC machining services, CNC rapid prototyping, forging parts machining, etc.